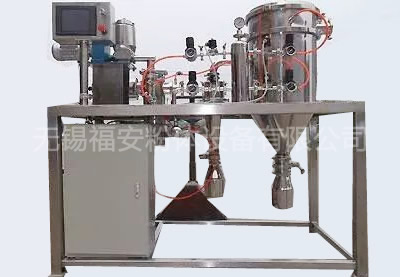
The characteristics of the system composition :
The JSF series high precision turbine classifier is mainly composed of feeding control system, classifier of classifier, high efficiency cyclone collector, pulse bag collector, high pressure fan and electrical control system.
(1)Feed control system. The feeding control system is composed of a uniform feeding machine and a feeding silo, and the continuous and uniform feeding is controlled by adjusting the amplitude of the vibration feeding and the speed of frequency conversion. The inner wall of the system is all pasted with polyurethane, so as to prevent the contact between the material and the metal.
(2)
The main machine of the classifier. The main engine of the classifier consists of the motor, the head, the grading wheel, the coupling, the cone reflection cone, and so on. By adjusting the speed of the grading wheel and combining with the two inlet air, the reasonable gas solid concentration can be realized, so that the particles and the air flow are dispersed to the material effectively. The grading impeller is made of zirconia ceramics. Zirconia is hard and brittle. If it needs to be removed, it must be put gently to avoid breaking. All the inner walls of the cylinder are pasted with alumina ceramic sheets to avoid contact with metal and wear resistance. The impeller of classifier is adjusted by frequency converter, and protection measures such as loss of pressure protection, overload protection, operation state monitoring and alarm system are designed.
(3)High efficiency cyclone collector. The equipment is the three stage collection system in the grading products. After the dust air flow into the cyclone collector, the powder falls along the wall of the cylinder and is separated at the tail end of the inner cone because of the centrifugal force. The purified gas is then discharged to the dust collector with some fine particles passing through the central tube of the cyclone. The inner wall of the cyclone is all pasted with polyurethane
(4)
Pulse bag type dust collector. The equipment consists of a bag collecting device, a pulse cleaning device and a pneumatic control device. The bag collection system is made up of our imports of advanced peritoneal filter bags and Wen Qiu aluminum pipes. Due to the characteristics of the material, the specific gravity and the concentration of the brittle gas and solid are different, and the design filter area is different. All the walls of the duster are covered with polyurethane.
(5)Electrical control system. The electrical control system is mostly designed with brand components, which makes the equipment more intelligent and makes the operation of the complete set of equipment simpler. The system can also use advanced touch screen and programmable PLC controller to fully realize automatic control.
Working principle
The classifier and cyclone separator, dust collector and induced draft fan form a classification system. Under the action of the fan pumping force, the inlet of the lower end of the classifier moves to the classification zone with the updraft, and it separates the coarse and fine materials from the strong centrifugal force produced by the high-speed rotating classification turbine. The fine particles that meet the requirements of the particle size are collected through the clearance of the gradation wheel into the cyclone separator or the dust collector, and the coarse particles are collected. After the entrainment of some fine particles, the velocity disappears and goes down to the two tuyere along the wall of the cylinder. The coarse and fine particles are separated by the strong cleaning effect of two times of wind, and the fine particles are raised to two grades in the classification area, and the coarse particles are dropped to the discharge port.
Maintenance and maintenance of equipment
1. Note
A feed volume should be determined according to the size of the host load: the main engine load is too large, then the feed should be reduced; the amount of feed should be increased to ensure the normal operation of the main engine under the rated load.
B the fineness of the powder produced in the complete set of equipment can be adjusted in a certain range according to the requirements of users. If the product is coarse, the speed of the grading impeller can be adjusted to meet the requirement. Conversely, if the fineness of the product is too small, the speed of the grading impeller can be reduced appropriately.
The pulse bag filter is cleaned by continuous automatic ashing.
C processes heat sensitive material, the main motor load should be adjusted to a slightly lower rated power value.
The size of the air flow in the D conveying pipe can be realized by adjusting the opening degree of the damper door. When the air volume is large, the size of the product becomes coarser, but the output increases, and vice versa. When air volume has met the requirements of product fineness and productivity, it is no longer adjusted.
E should regularly check the tightness of the triangle belt to prevent the belt pulley from slipping.
The sudden reduction of the pressure of the F air compressor indicates that the nozzle of the equipment is relatively worn and needs to be replaced immediately.
G requires that raw materials such as metals and high hardness can not be contained in graded raw materials. If these inclusions enter the classification chamber, they will cause serious damage.
Before the H drives the machine, it should be checked whether the joint parts are loose, the interface is sealed well, the indoor has not fallen into the metallic material, the rotation part is flexible, if there is abnormal phenomenon, it should be removed and the machine can be opened.
I the rotation direction of each motor must be rotated in the prescribed direction.
J shall lubricate and lubricate strictly according to the lubrication regulations, but the special molybdenum disulfide grease for the machine must be added, and it is strictly prohibited to mix with other lubricating grease.
K should strictly check whether the water content of the material is within the prescribed range before starting operation, so as not to affect the product quality and production efficiency (generally require less than 0.5% water content)
L before checking the production process, check whether the belt drive shroud is fastened. Do not remove the transmission shroud and run.
M when examining the direction of motor operation, it is strictly prohibited to start the motor with hand or stick stick to contact the belt to identify the direction of the motor running
N keeps all the sanitation around the appliance at any time. It is strictly prohibited to put sundries around all the electrical appliances in order to avoid the short circuit of the electric appliance or the body.
the operator's body around the damage caused by the belt transmission.
O cleaning equipment, if you need to disassemble the equipment, you must turn off the total power supply in the electric cabinet. It is strictly prohibited to start the appliance.
when the equipment is split.
P in the production process is strictly prohibited to hand or stick sticks into the discharge port, so as to avoid the risk of crushing or breaking
In the process of production, Q is strictly prohibited to open the electric control cabinet. If the circuit problems are closed, all the electrical appliances must be shut off first. After the power break, reprocessing to avoid the electric shock danger of the operation workers' misoperation of the circuit, the non professional people strictly prohibit the change of the circuit.
in the electric control cabinet.
R do not sprinkle water on motor and bearing seal when cleaning.
S when you need to replace damaged parts and repair, first open the electric valve, hang the valve label, then clap your hands in the following order.
T lubrication / regular refueling
The bearing lubrication must be made of high speed special grease, which accounts for about 1/3 of the bearing ring, and the cycle of replacing molybdenum disulfide grease is as follows: the classifier must be refueling after 1500 hours of work.
Refueling tool: a gas gun.
Air compressor maintenance must be strictly in accordance with the instructions of air compressor, regular maintenance, and special oil for air compressor.
2, auxiliary equipment
(1) equipment maintenance for draught fan, unloading valve and dust collector shall be carried out according to the corresponding specifications;
(2) the new equipment must adjust the length of the transmission belt after 100 hours of operation to ensure the tightness of the belt;
2.1 grader
(1) for each running 3000h, the wear condition of grading impeller should be regularly checked;
(2) the grading wheel bearing is a high precision and fully sealed bearing. After running 1000h, grease must be added. If it is found loose and loose, it must be replaced in time;
2.2 deduster
(1) under the condition of the normal operation of the pulse injection controller, the negative pressure of the system should be constant in a certain range. If the change is too large, it is necessary to clean the bag or replace the new bag;
(2) regularly observe whether there is any dust in the outlet of the fan, whether the bag is damaged or not, and deal with it in time;
2.3 electronic control system
(1) the electrical control cabinet should pay attention to dust prevention, use the control cabinet door tightly to prevent dust from entering, regularly clean up the dust and prevent bad contact;
(2) pay attention to water and moisture, keep control cabinet dry;
2.4 other
(1) lubrication: Lubrication of main and auxiliary machines should be checked regularly, lubricating oil should be added in time;
(2) regularly check the tightness of the equipment, the temperature of each motor, whether the wire is hot or not, and deal with it in time;
(3) after 600 hours of operation, all equipment should be shut down for overhaul and maintenance.
3 Replacement of the bearing of a classifier
In the process of bearing installation, the following procedures should be strictly followed. During the operation, it is strictly prohibited to hammer directly on bearings and shafts with steel hammers. The installation steps of the bearing are as follows:
The first step is to wash the new bearings with gasoline or diesel oil and dry them. During the washing process, there is no dust left in the bearing ball and ball socket.
Second step, remove the damaged bearing
First, use special tools to pull out the grading wheel and pulley, then take the upper and lower bearing cover down, and then hammer the spindle from the upper bearing to the bearing end until the bearing box is knocked out of the upper and lower bearings.
After the bearing and shaft knock out the bearing box, use special tools to strike the inner ring of the bearing, take the damaged bearing down from the shaft, and wash the position of the bearing with gasoline or diesel.
Check whether there is any sundries in the bearing box, if there are any sundries, clean them before installing new bearings.
Note:
1. when knocking the spindle, when the upper bearing moves to the lower bearing hole position, it is necessary to carefully counter the rear bearing and knock out the bearing hole.
2. when striking the spindle, it is forbidden to hammer the spindle directly with hammers, and to place copper rods between the hammer and the spindle;
Third step, will wash, dry after the bearing and grease (attention: grease is best to fill the bearing 1/3 to 1/2); the upper and lower bearing cover groove inside the grease clean clean, and the grease, to fill the groove of 2/3 suitable;
Note: the grease should be selected at 200 degree high temperature,
The fourth step is to load the upper and lower bearings loaded with grease (mounted on the spindle and percussion in place (located on the steps on the main shaft);
Note: 1. the order of the replacement of the upper and lower bearings is strictly prohibited;
2. it is strictly prohibited to install the upper and lower bearings in reverse direction, and the lower side of the bearing bearing down to the side of the wide side (toward the pulley direction);
3. when loading bearings, it is strictly prohibited to beat the outer ring of the bearing at will. The inner ring of the bearing must be struck with special tools;
In the fifth step, the spindle of the bearing is knocked into the bearing box from the bearing direction of the upper bearing to the lower bearing; the knocking method and the notices are the same as the second steps; when the upper and lower bearings are all entered into the bearing box, the bearing cover is installed and the bearing cover is fastened to the bearing end of the lower bearing and the bearing end of the lower bearing cover, so that the lower bearing is in place; Use the special tool to strike the bearing's inner and outer ring at the same time, so that the upper bearing is in place, then the upper bearing cap is loaded and fastened.
Attention: first from the top down to the main shaft to make the lower bearing in place to make the upper bearing in place, and when the bearing is knocked on, the inner and outer ring of the bearing must be struck with a special tool at the same time;
Sixth step, bearing installation, reloading pulley and grading wheel;
Common fault and troubleshooting
Fault |
Reason |
Treatment measures |
The current of the classifier is high or unstable |
1.High or unstable feed volume
2.System negative pressure deficiency
3.Inhomogeneous feed grain size |
1.Reduce or stabilize the amount of feed
2.Check out of system pressure
3.Keep uniform feed size |
System negative pressure deficiency |
1.The bag cleaning strength is not enough
2.Cloth bag wet
3.Out of time |
1.Increase the pulse frequency or pulse width
2.Eliminate water in the system in time
3.Leave the material in time (1 times every 5-10 minutes) |
The products have too large particles |
1.Unevenness of feeding
2.Too little machine memory
3.Low speed of grading wheel
4.Air leakage at the junction of the system |
1.Set the vibration frequency of the feeder to ensure uniform feeding
2.Proper amount of machine memory
3.Adjust the rotational speed of the grading wheel properly
4.Seal condition at the connection of the system |
Scalding of grade wheel bearing |
1.Poor lubrication
2.Bearing powder
3.分级轮动平衡失效 |
1.Repress the maintenance requirements with the lubricant
2.Cleaning the dust in the labyrinth of the classification wheel and maintaining the dust in the labyrinth
3.Redoing grading wheel dynamic balance |
A large amount of dust in the outlet of the fan |
1.Filter tube breakage
2.Leakage of the interface between the cartridge and the floral plate |
1.Check and replace the damaged filter cartridge
2.Sealing interface |